Specjaliści z KGHM CUPRUM wspólnie z firmą „Kamienna” zrealizowali projekt, który miał na celu stworzenie pilotażowego procesu produkcyjnego dla zakładu kamieniarskiego.
Proces ten rozpoczął się od precyzyjnego pomiaru obiektu będącego przedmiotem zlecenia, metodą skanowania laserowego, następnie przechodząc w fazę projektowania elementu z kamienia, jego wizualizacji w wirtualnym Showroomie, po produkcję z wykorzystaniem maszyny obróbczej CNC.
– W tym ciekawym przedsięwzięciu współpracowaliśmy z mikroprzedsiębiorstwem, tworząc nowoczesną, proekologiczną linię produkcyjną, przystosowaną do pracy osób niepełnosprawnych i zgodną z ideą zrównoważonego rozwoju – podsumowuje Miłosz Becker, kierownik projektu z ramienia KGHM CUPRUM – Odnieśliśmy sukces zarówno w zakresie rozwoju metod i narzędzi pomiarowych (precyzyjny skaning), podniesienia własnych kompetencji, jak i w procesie wsparcia mikroprzedsiębiorstwa we wdrożeniu nowej technologii.
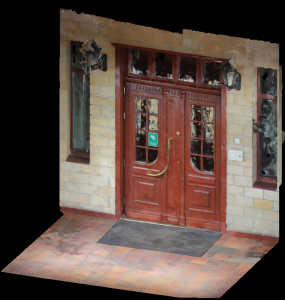
Rzeczywisty model 3D wejścia do budynku
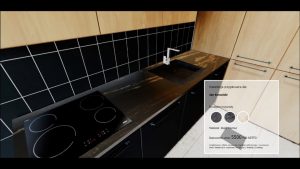
Wizualizacja kamiennego blatu kuchennego
Połączenie metod pomiarowych skaningu oraz fotogrametrii pozwoliło na modelowanie obiektu dla klienta w postaci realistycznej siatki rzeczywistości, stanowiącej tło dla wizualizacji projektowanego elementu kamiennego, dzięki czemu możliwe było wiarygodne zasymulowanie efektu końcowego planowanej inwestycji. Ponadto precyzyjny pomiar obiektu pozwolił na zaprojektowanie zamawianych elementów z uwzględnieniem wszelkich niedoskonałości i krzywizn, takich jak brak kątów prostych w narożnikach ścian czy brak ich płaszczyznowości. Następnie element ten został wycięty w pełni automatycznie przez maszynę CNC i praktycznie był gotowy do instalacji bez konieczności wykonywania dodatkowych poprawek.
Linia produkcyjna oparta jest na idei zrównoważonego rozwoju, redukując maksymalnie straty materiału oraz wykorzystując wodę deszczową jako wodę technologiczną pracującą w obiegu zamkniętym. Odpady powstające przy produkcji przerabiane są na kruszywo. Cała linia przystosowana jest również do obsługi przez osoby z niepełnosprawnościami.
Ostatnim założeniem projektu było wprowadzenie oszczędności związanych z obsługą nowoczesnych maszyn CNC. Koszt ich pracy jest niewspółmiernie mały w porównaniu do kosztów postoju związanego z awarią. W celu przewidywania awarii zanim jeszcze wystąpią, opracowano metodę cyklicznych pomiarów warunków geometrycznych głównych elementów ruchomych maszyny, w celu zapobiegania awariom spowodowanym odkształceniami tych elementów.
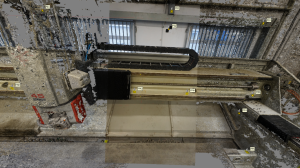
Pomiary kontrolne maszyny CNC (fotogrametria)
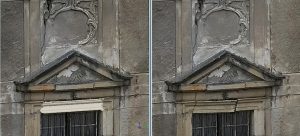
Wizualizacja naprawy uszkodzonego elementu architektonicznego
Projekt pn. „Zintegrowany system obróbki surowca skalnego. Proekologiczna linia produkcyjna, oparta na idei zrównoważonego rozwoju i dostosowana do obsługi przez osoby niepełnosprawne”, zrealizowany został w ramach Regionalnego Programu Operacyjnego Województwa Dolnośląskiego na lata 2014-2020, współfinansowanego z Europejskiego Funduszu Rozwoju Regionalnego (Umowa RPDS.01.02.01-02-0040/20-00).